In the context of increasingly high automation demands in industrial manufacturing, the integration of advanced technologies such as 3D cameras and industrial robots has become critically important. The solution of combining 3D cameras with industrial robots for product picking helps optimize the production process, enhance accuracy, and improve operational efficiency. These technologies not only increase productivity but also minimize the risk of errors in manufacturing.
1. Solution Architecture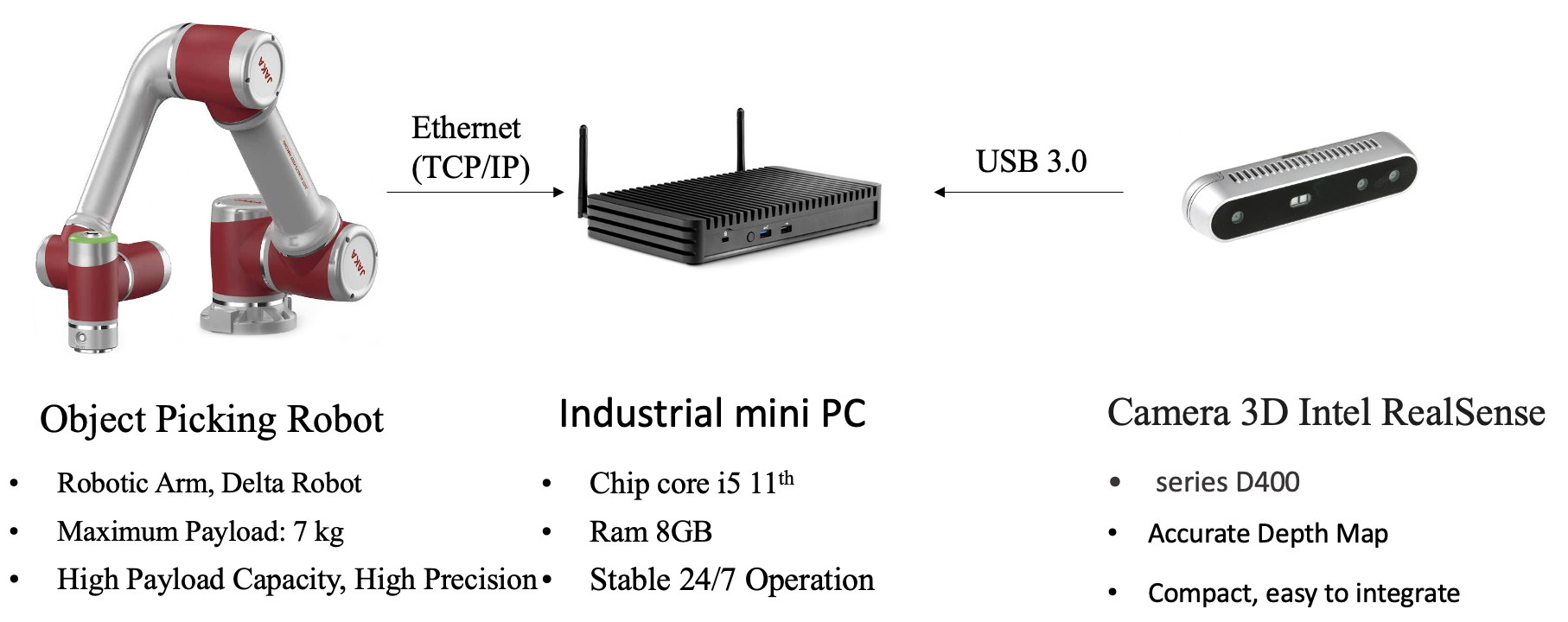
The system consists of an Intel RealSense 3D camera, a pick-and-place robot, and control software. The robot performs the picking operation, while the software processes and manages the entire workflow.
2. Camera 3D Intel RealSense
Camera 3D Intel Realsense D415
The camera provides 3D point cloud data and color images, enabling the robot to accurately identify objects
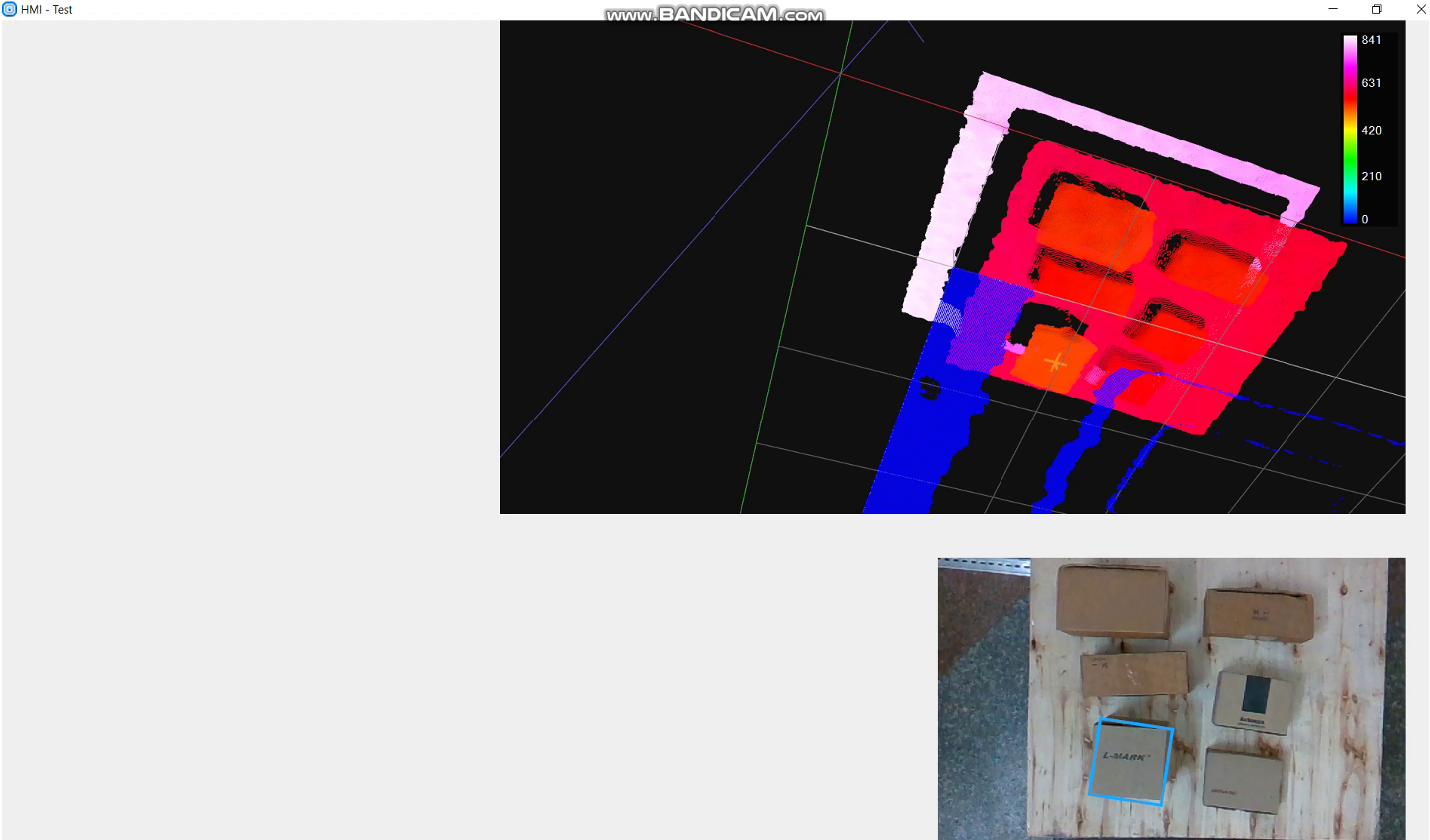
3. Processing computer
Asus® NUC Rugged Chassis Element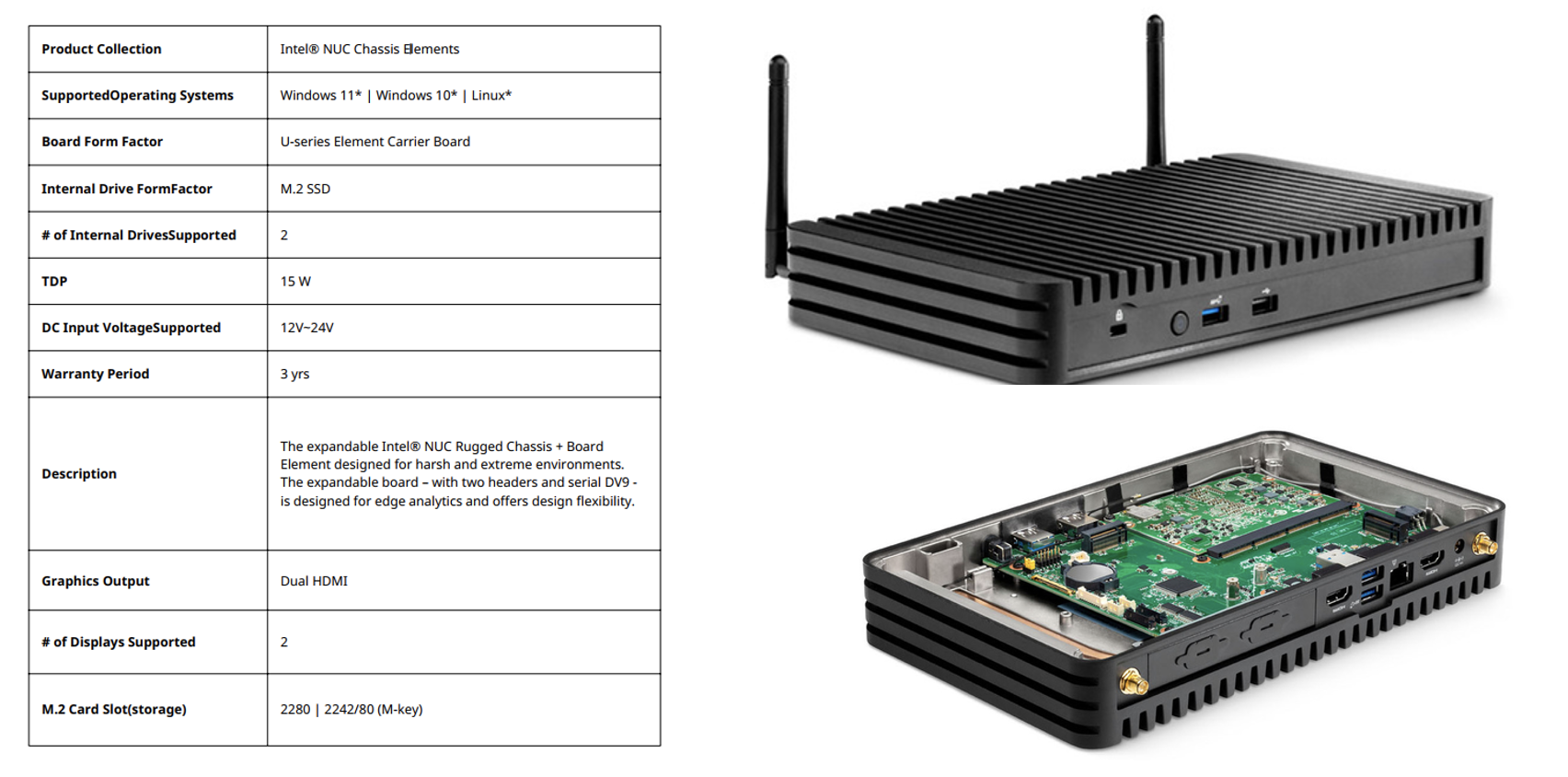
4. JAKA Zu 7 Robot System
With the robotic arm and 3D camera, we can perform the following tasks:
- Replace manual labor in stages where the products fed into the system are not yet sorted.
- Help reduce time and intermediate steps for automatic feeding into the system.
- Accurately identify products that are mixed up in trays.
- Integrated camera programs, just install and use, help minimize programming time and processing steps.
Cycle of Object Grabbing Robot Using 3D Camera
-
Image Acquisition
The Intel RealSense 3D camera is used to capture the three-dimensional images of the working area.
The data includes:-
Color image (RGB)
-
Depth data
-
Point Cloud
Preprocessing & Feature Extraction
-
Clean up the point cloud data (denoise, downsample)
-
Segment the background and the object to be grasped
-
Compute geometric features (size, centroid, orientation…)
Object Detection & Pose Estimation
-
Use object detection techniques and algorithms.
Results: -
Identify the type of object
-
3D coordinates and rotation angles (6 DOF pose)
-
Detection time: 1-2 seconds
-
Graspable object size: 4cm x 2cm
Grasp Planning & Motion Planning
-
Determine the optimal grasping position (grasp point)
-
Use motion planning algorithms (MoveIt, OMPL, RRT, TrajOpt…)
Execution
-
Send control commands to the robot
-
The robot moves to the grasping position → grabs the object → moves to the target location
Feedback & Error Handling
-
Force sensors, camera, or tracking system to confirm successful grasp
-
If the grasp fails, repeat the detection and planning steps
-
Cycle time for object grabbing robot: 3-5 seconds
-
Real-World Applications
Solution Deployment Timeframe: 2–3 months
Contact Information
Address: No. 76, Alley 120 Yen Lang, Dong Da District, Hanoi
Hotline: +84 888627888
Website: www.brandpc.vn
Youtube: https://www.youtube.com/@brandpcVN
Fanpage: https://www.facebook.com/BrandPCVietnam